3 Ways Vehicles Are Reducing Weight
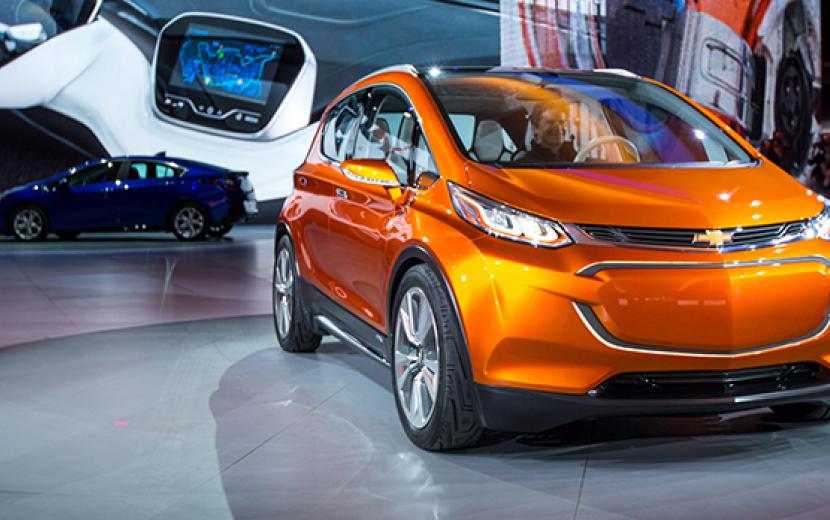
Electric Vehicles
Electric vehicles, like the Chevy Bolt, use materials such as aluminum, magnesium and carbon fiber to drive down curb weight.
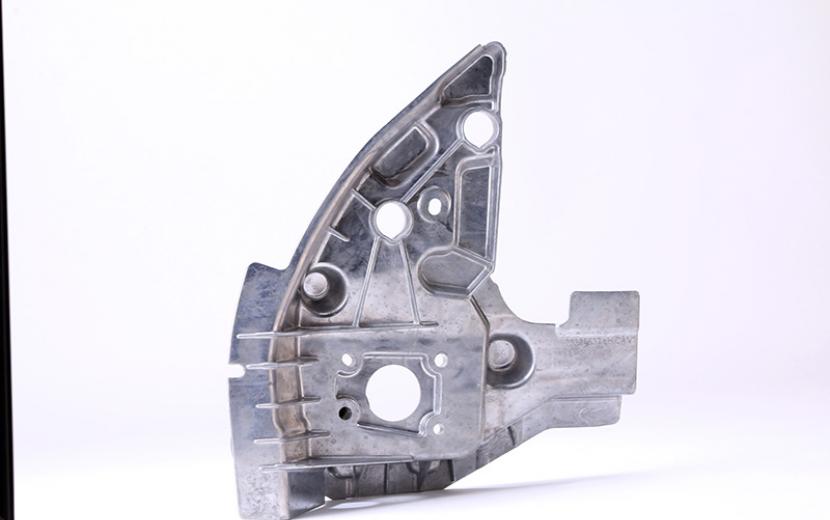
Vacuum Diecasting Replaces Steel Stamping
Part Count Reduction: 5 pieces to 1.
Weight reduction: 20% mass savings.
• Vacuum diecasting creates high quality parts with high structural integrity.
• The aluminum casting design gave engineers flexibility to design more efficient attachment points.
• Smart tooling design helped the supplier make more parts per cycle.
Weight reduction: 20% mass savings.
• Vacuum diecasting creates high quality parts with high structural integrity.
• The aluminum casting design gave engineers flexibility to design more efficient attachment points.
• Smart tooling design helped the supplier make more parts per cycle.
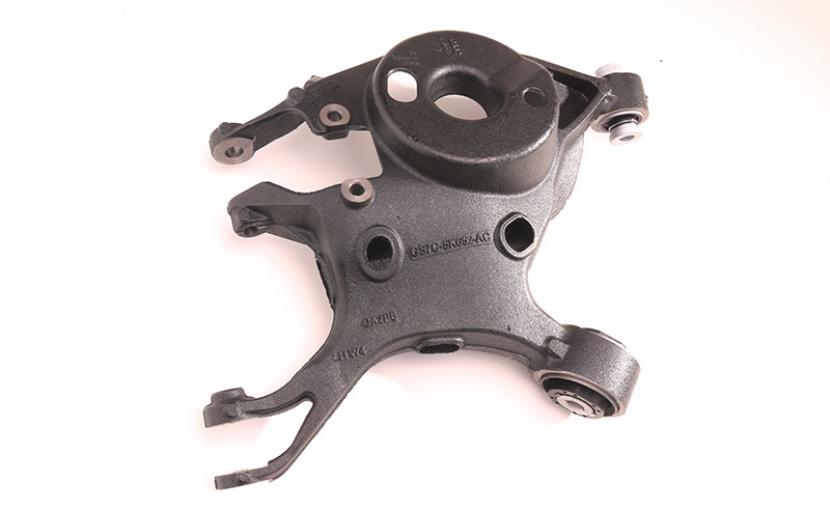
Ductile Iron Replacing Aluminum
Part Count Reduction: Same.
Weight reduction: 6 lbs.
• Hollow design helped reduce mass.
• The ductile iron alloy chosen offers high ductility and toughness so thinner walls could be used.
• Casting solidification simulation ensured a smooth and rapid setup for production.
Weight reduction: 6 lbs.
• Hollow design helped reduce mass.
• The ductile iron alloy chosen offers high ductility and toughness so thinner walls could be used.
• Casting solidification simulation ensured a smooth and rapid setup for production.
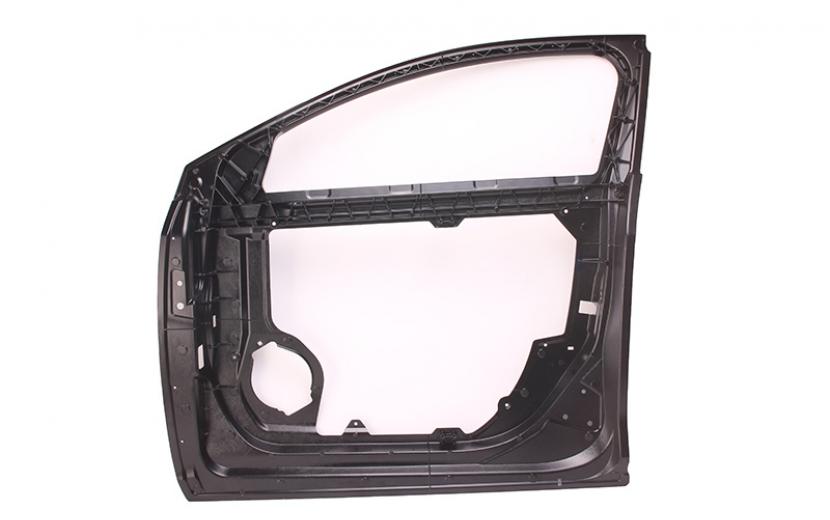
Steel Stamping to Magnesium Casting
Part Count Reduction: 7 parts to 2.
Weight reduction: 19.4 lbs.
• Elimination of spot welding.
• Strengthening ribs for required stiffness with less overall mass.
• Fluidity of magnesium made casting thin sections possible.
• Tool designed with internal heating and cooling to aid solidification.
Weight reduction: 19.4 lbs.
• Elimination of spot welding.
• Strengthening ribs for required stiffness with less overall mass.
• Fluidity of magnesium made casting thin sections possible.
• Tool designed with internal heating and cooling to aid solidification.
Ford and General Motors worked with their casting suppliers to reduce vehicle weight with a variety of methods, from replacing material to switching processes.