Wrench Castings Tighten Up Safety
Hold a metal casting in your hand today and there’s a good chance it’ll be hidden tomorrow.
Most castings quietly serve their mission undercover, tucked inside something larger and more complex than themselves. So, when a tool that’ll be wielded in human hands on a jobsite every day winds up as a casting, it’s cause for a little pause.
Every now and then, that’s what engineer Gary Jackson at LA Aluminum (LAA) does when he’s sitting in his office and picks up a brightly painted industrial wrench, one of two unique types he helped create.
“You can get into the philosophical details of it,” he said, “but you feel something internally when you’re holding a tool.”
The team at the Hayden, Idaho-based foundry, an AFS Corporate Member, worked with Bernie Hunt, managing partner of Mountain Valley Supply (MVS) in Grand Junction, Colorado, to convert a weldment of Hunt’s concept into a solid aluminum casting for the oil and gas industry his company serves––that tool is the one-of-a-kind Lift Wrench 714.
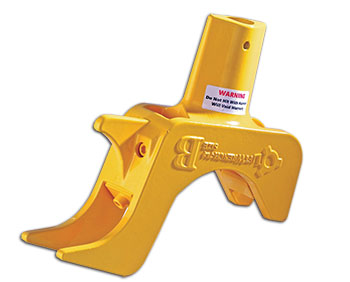
unique but simple functions of first lifting heavy
pipes off the ground, then enabling workers to
loosen or tighten union connections instead of
swinging blows to the unions with a sledgehammer.
Its name points to the simple but significant dual functions it performs out on an oil field or fracking site, enabling a worker to lift pipes on the ground to rest on a wooden skid (block) and then turn the union to connect pipes together that run to wells. And the number 714? That’s the birth date Hunt and his sales colleague Brett Harris share, giving the tool a special crest of family identity, as it were.
What makes the Lift Wrench 714 so special is how it solved a specific problem for oil and gas companies, which were turning to Hunt for answers back in 2014. Until now, the way these workers loosen and tighten pipe unions has been physically hazardous: They slug away at the unions with a sledgehammer, and in the process frequently smash knees, legs, hands and fingers, with the added strike of hurting their backs both from the bashing movement as well as stooping to lift up pipes by hand. Hunt recalls the management at one well-known oil company revealing that, at one point, they had 12 men out due to sledgehammer-related injuries.
Add to these detriments the fact that the unions don’t fare well in these violent encounters and must be frequently replaced at sizeable annual cost, and you’ve got an equation for frustration.
Once he realized the scope of the conundrum and that no satisfactory device existed in the marketplace, Hunt partnered up with his friend and business associate, Steve Heifner from Bulldog Energy, to first develop a steel weldment, which was too heavy, followed by a 6061-aluminum weldment of the Lift Wrench, of which MVS sold a few. But the onerous manufacturing required per unit wasn’t sustainable if they were going to achieve mass production and get the tool out where it’s needed.
“Steve had a fabrication company so we took aluminum, because we needed it to be light weight, and we were cutting and welding it,” said Hunt. “And it just took forever to actually make one piece. That’s when we started looking at other avenues.”
Creation headaches aside, the fabricated Lift Wrench was failing in field tests, breaking at a weld point. With some research, Hunt discovered aluminum loses 50% of its strength when welded, thus throwing another monkey wrench into their progress.
Next stop: Find a designer. When the Lift Wrench makers met Mechanical Design Engineer Matthew Kibler, the lightbulb clicked on as they jointly concluded: This tool was only going to see the light of day as a casting.
Enter LA Aluminum, which won the project on price according to Hunt, but LAA Sales and Marketing Manager Sarah Oswald said there may have been more behind Hunt’s decision.
“We have a really good reputation for quality work and customer service,” she said, “and I also think maybe they selected us because of our willingness and dedication to partner with them on their design ... I think it was probably the commitment between our two companies that made it an ideal fit.”
Today, LAA makes seven different part numbers for MVS. Hunt, MVS’s owner, said he’s proud of its made-in-the-U.S.A. distinction, as well as being the only hammer union wrench on the market that both lifts pipe and turns unions. Retailing at $650 for the 2-inch wrench, $750 for the 3-inch, and $850 for the yet-to-come 4-inch, the Lift Wrench, as a casting, turned out to be a major money-saver for Hunt.
“This will probably floor you, but we had about a 65% savings by going with the casting over the weldment,” he said. “Now, the upfront cost was a lot more. But it doesn’t take long to pay off the upfront cost with the savings we acquired per wrench.”
Worth the Work
Starting in 2017, LA Aluminum worked closely with Kibler to develop a cast-friendly design to be manufactured via the permanent mold casting process, which is highly efficient for repeatable, high-volume jobs, with 356 Aluminum T6 alloy, a particular area of expertise at LAA.
“Matt’s a really great designer and an excellent guy to work with,” Jackson said. “He built a robust model that we were able to modify for casting pretty effectively. When you get a part you have to make into a casting, there’s a lot of little details you have to put into it, and there was definitely a lot of back and forth.”
Twelve weeks, 114 email exchanges and dozens of phone calls later, the first of three eventual Lift Wrench 714s emerged as a brightly powder-coated, fully machined and assembled tool ready to sell and ready for active duty protecting human limbs and preserving union life. Two of the assembled wrenches require steel wear plates and Heli-coils on the handles, Oswald said, and the foundry also assembles quick release pins and a lanyard.
Together with Oswald, Jackson, who is manufacturing process engineer and manager of quality at LAA, led a small foundry team comprised of the company’s plant manager, tooling supervisor and a tooling designer to execute the casting; it was not without challenges.
At first, a heavy section in the casting was causing a little shrink, Jackson recalled, which resulted in the downstream problem of the material “hanging up” in one side of the mold––aka sticking and not releasing clean from the mold. Numerous tweaks and corrective steps resolved the issue.
“We had to take a really close look at wall thickness and parts thickness all over the casting, trying to get everything uniform,” said Jackson. “There was a little bit of lightweighting, pulling material away to get things to a certain thickness just to make it flow nicer. We were looking at it from a flow standpoint, but it also happened to knock half a pound off the part.
“We also had to innovate a pretty interesting shell core––we had to put an extra mechanism onto the shell corebox to make it come out right,” he added. “And we had to develop a secondary process to the shell core. So, as far as casting quirks go, we had to do everything to this casting to get it to work.”
Lasting Impression
The real war of wits was won in the knurling, which involves adding a waffle pattern on the tool handle for good grip. It’s a common practice in machining, according to Jackson, but a perplexing puzzle to design into the casting itself. “But once you do it,” Oswald added, “you’ve got it on every part,” thus cutting machining time substantially.
“This was actually a fun challenge for me,” Jackson said. “It took quite a bit of time to really figure out how to lay down knurling and make it cast-friendly. “It required putting the mold halves in the CNC mill and, with a very tiny tool, etching little lines over and over again ... to cut the knurling pattern into the mold.”
In the end, the knurling itself is the object of Jackson’s greatest pride from casting the Lift Wrench 714. “It was the result of a lot of effort,” he said, “And it feels really, really good to hold one of these. For a while there, I was actually walking around the foundry with one of these and l was saying, ‘Hey, here, hold this. This feels amazing!’”
It’s fitting that, with the knurling, he inadvertently left his own personal mark on the finished wrench.
“I geek out about this, but if you watch the YouTube video [demonstrating the Lift Wrench], when the fellow holds up the wrench handle you can see there are little dark smudges––those are my fingerprints,” Jackson said. “I get to see a product that’s going to help people, and it will forever have my identity on it.”
Hunt said feedback from the field has been excellent, and his customers––some of the largest oil and gas companies across three countries––are buying up the Lift Wrench 714 at a pace of 100+ per order every few months. Weighing 7.7 lbs., according to Oswald, it packs an astonishing 6,600 lbs. of force. Ironically, sledgehammers have more force, but one miss and that’s a few tons of ouch.
“The young ones coming in who are trained with it, those guys absolutely love it,” Hunt said. “You couldn’t get them to use a [sledge]hammer if you wanted to.”
Far From Finished
A job well done deserves another, and it wasn’t long before Hunt was cooking up a new solution for an oil company––and bringing a second casting concept to LAA’s doorstep.
While calling on his customer at Occidental Petroleum to sell the Lift Wrench 714, Hunt said an equally vexing sledgehammer-related problem surfaced in the conversation. Turns out, hammer unions connecting 3- to 5-inch, low-pressure suction hoses receive the same beating as pipe unions, but in this case, the entire hose is constantly having to be replaced at a cost of $400-$500 a pop, he said.
Responding to the request for help, Hunt rushed back to the drawing board with designer Kibler and created a design for the Hose Wrench in late 2017. By early 2018, the innovative aluminum casting, like its bigger cousin, achieved light weight (just over 4 lbs.) and sufficient strength to loosen and tighten hose unions with zero damage to man or metal.
Made in three sizes to fit 3-, 4- and 5-inch unions, the Hose Wrench sells for $450. Because they’re castings, the per unit cost to make them at the foundry is far less than Hunt would’ve paid to cut and weld each piece, he said.
And mass producing is cake.
With the Lift Wrench under LAA’s belt, most technical challenges resolved, and a well-forged working relationship with MVS firmly in place, the Hose Wrench casting process was faster and smoother, but not entirely without lumps.
“In contrast to the Lift Wrench 714, the Hose Wrench had some big geometrical challenges to it with its own integrated handle,” Jackson said. “It would be a little bit of a different animal than the Lift Wrenches previous to it.
“There was a whole huge heavy section on top of a really thin section, and castings like that don’t typically play nice,” he continued. “The biggest challenge with this one was actually doing a pocket in it and lightweighting––not so that we could necessarily lightweight; that was a side effect. The primary issue was just making more uniform wall thickness so we could optimize the casting ... we didn’t have the same kind of struggles; just a little geometry change, and they came out really, really well.”
Time, of course, was of the essence, and LAA pulled through with finished, powder-coated product in a much tighter timeframe than the first project. But meeting tough deadlines was rote by then––even during previous production on the Lift Wrench, when Hunt called from a tradeshow in Texas and asked for three wrenches overnight, LAA hustled and got the samples there the next day.
“I have to say that our team, especially our design team, really rose to the challenge,” Oswald said. “Bernie would say, I need product here tomorrow, and I don’t even know how we made it happen but we made it happen. I’m really proud of our team.”
In the end, both of MVS’s wrenches were cast in collaboration and coated in deep satisfaction.
“We helped solve a problem that is not only bigger than ourselves, but ultimately is keeping people safe,” Oswald reflected. “Knowing we are part of this bigger picture, knowing that what we’re doing is contributing to the overall safety of an industry, is just an overwhelming feeling.” CS
Click here to view the digital edition.