2019 Casting of the Year Winners
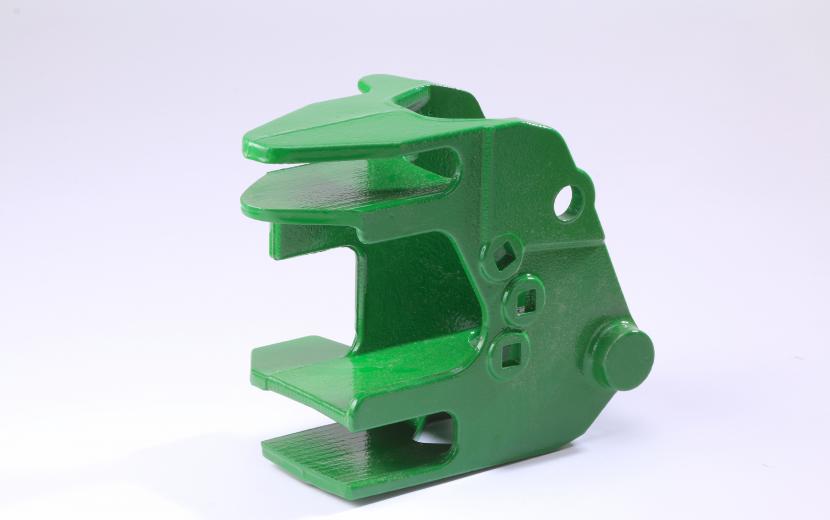
CASTING OF THE YEAR
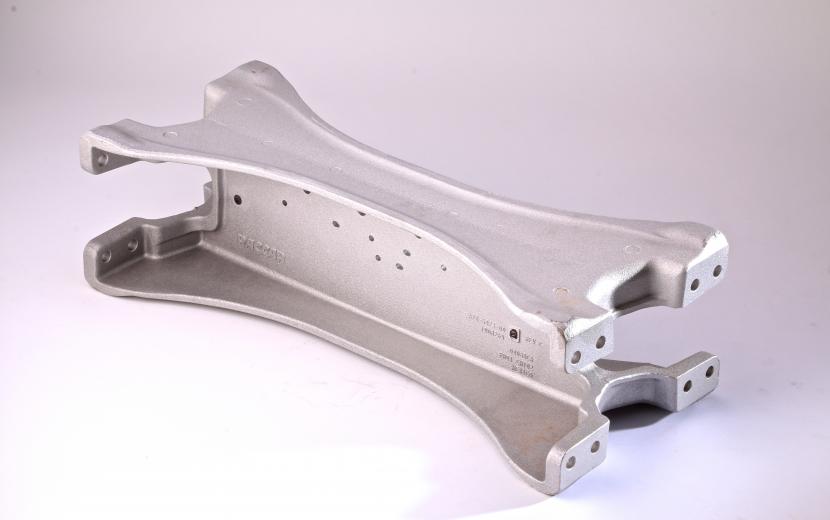
NEWCOMER OF THE YEAR

ACHIEVEMENT BY A SMALL FOUNDRY
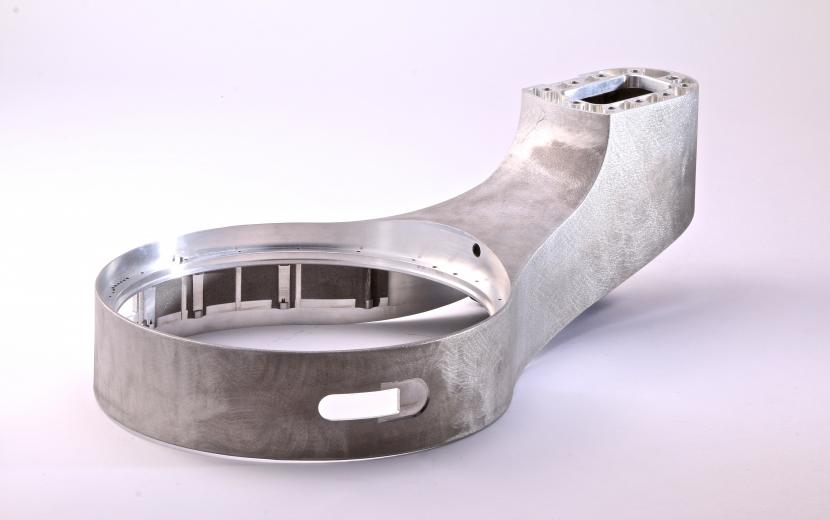
BEST EXAMPLE OF A CASTING CONVERSION
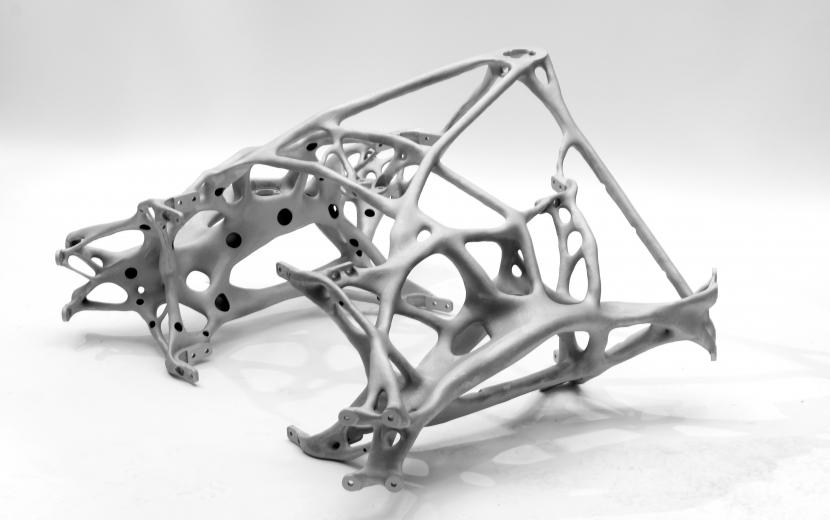
BEST PROTOTYPE OR INNOVATION

OUTSTANDING ACHIEVEMENT
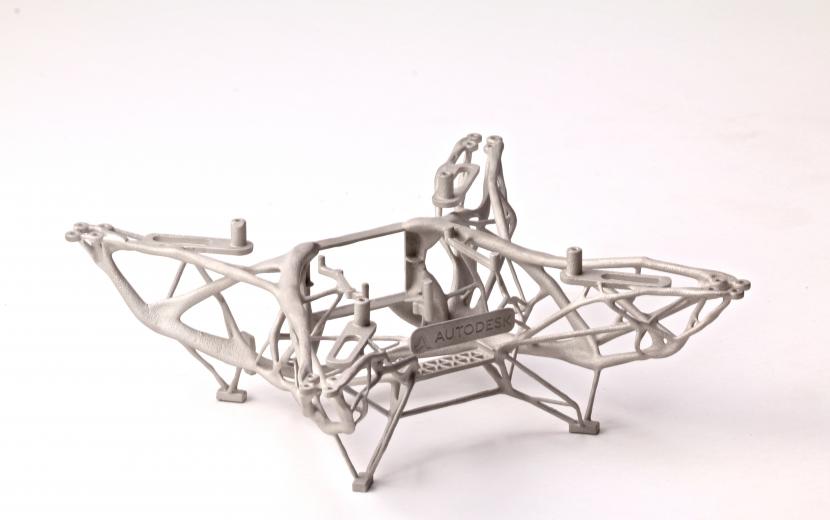
OUTSTANDING ACHIEVEMENT
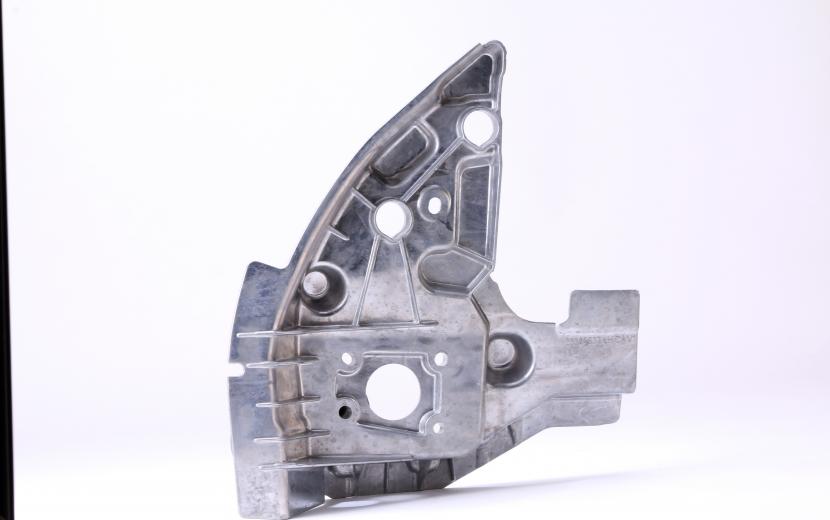
OUTSTANDING ACHIEVEMENT
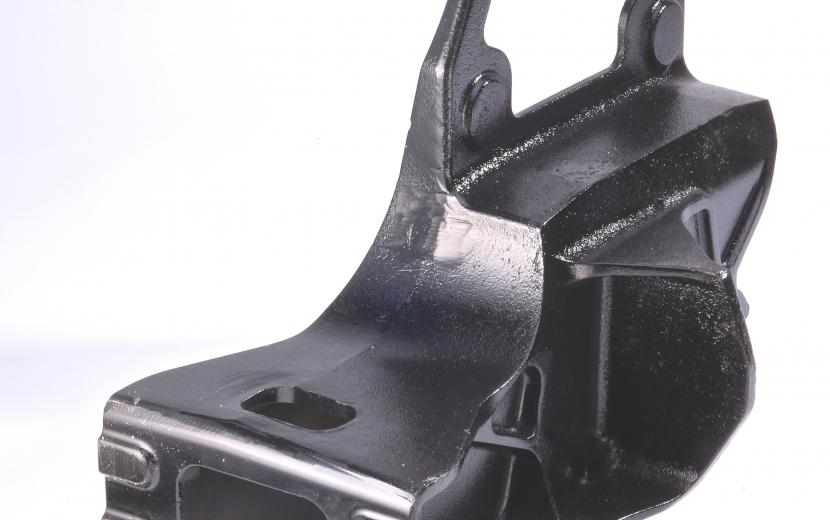
OUTSTANDING ACHIEVEMENT
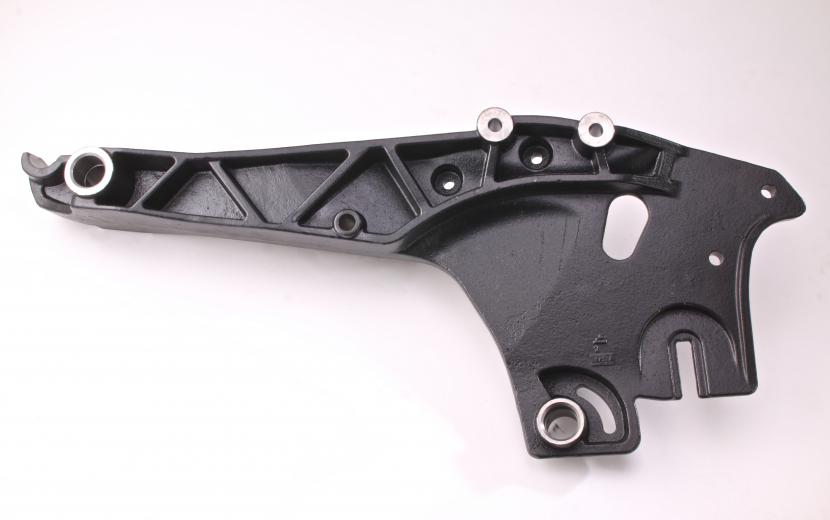
OUTSTANDING ACHIEVEMENT
The annual Casting of the Year competition is sponsored by the American Foundry Society and Metal Casting Design & Purchasing magazine and recognizes excellence in casting design. The competition is open to all North American metalcasters and designers/end-users of metal castings. Castings are accepted in all metals, casting processes, end-use applications, and sizes.
This year, four new categories were introduced to complement Casting of the Year. They were: Newcomer (Rookie of the Year), Best Example of a Casting Conversion, Achievement in a Small Foundry Business, Best Innovation/Prototype.
The winners are listed below.
CASTING OF THE YEAR
Swing Frame: Neenah Foundry
MATERIAL: Ductile iron.
PROCESS: Green sand.
WEIGHT: 25.6 lbs. (11.6 kg.), 23.2 lbs. machined (10.5 kg.)
DIMENSIONS: 12 x 8 x 6.5 in. (30.48 x 20.32 x 16.51 cm.)
APPLICATION: Small tractor backhoe attachment for light agriculture.
CUSTOMER: Amerequip.
Neenah’s casting design was developed based on Amerequip’s 11-piece laser-cut, welded assembly. The focus of the casting design was to improve quality and minimize cost. The casting was designed to be made using a single core in order to keep both tooling and piece price costs at a minimum. Assembly features, including holes and mating surfaces are machined into the casting instead of the current process, which uses laser-cut, welded pieces. This improves quality since the machined features can be held to tighter tolerances.
NEWCOMER OF THE YEAR
Bogie Crossmember: Consolidated Metco
MATERIAL: A-356 aluminum.
PROCESS: Permanent mold.
WEIGHT: 34 lbs.
DIMENSIONS: 33.4 x 13.5 x 9.6 in.
APPLICATION: On-highway semi trucks.
CUSTOMER: PACCAR.
Originally a five-piece aluminum extrusion assembly with 16 bolted joints, the crossmember supports frame loads and the trailer weight under the fifth wheel. This area of the chassis had not been cast before, but the foundry’s casting process parameters and a smart structural casting design made the conversion a possibility. The switch to a casting reduced the weight by 15 lbs., saved $10 per part and eliminated a significant amount of assembly time. The component passed all targets for stiffness and strength. In production now, a custom casting device used by the foundry enabled thin walls and holes to be cast.
ACHIEVEMENT BY A SMALL FOUNDRY
RF Cavity Center Section: Roman Manufacturing/Quality Non-Ferrous Foundry
MATERIAL: C110 Copper.
PROCESS: 3D printed sand mold.
WEIGHT: 110 lbs.
DIMENSIONS: 18 x 17.5 x 14 in.
APPLICATION: Particle acceleration.
CUSTOMER: Fermi National Accelerator Labs.
Due to the hollow structure and overall dimensions of this part, casting provides a substantial savings in both raw materials used and finish machining cost. Using 3D printed sand molds also allows for an economical process development and prototyping. The cavity center section, which is used on equipment that conducts experiments in high energy particle physics, was produced as a sand-cast copper casting in the late 1960s but since then had been machined or welded out of solid billet. This recent successful casting was the first attempt to return to the process in 50 years.
BEST EXAMPLE OF A CASTING CONVERSION
Halo: TPI Arcade
MATERIAL: A356 aluminum with a T6 heat treatment.
PROCESS: V-Process.
WEIGHT: 6.4 lbs.
DIMENSIONS: 28 x 14.5 x 8.25 in.
APPLICATION: Precision bearing housing for robotic surgery.
This component was originally designed as a part machined from billet and took advantage of the V-Process attributes to convert it to a casting. The casting has vertical (0 degree draft) and thin walls (.0125 in.) to minimize weight additions. Changing to a casting reduced cost by 80%, roughly $3,500 per part. The casting is produced with a 5% elongation in a T6 condition.
BEST PROTOTYPE OR INNOVATION
Interplanetary Lander Body Structure: Tooling & Equipment International
MATERIAL: A357-T6.
PROCESS: Low pressure sand.
WEIGHT: 69 lbs.
DIMENSIONS: 47.4 x 38.8 x 25.6 in.
APPLICATION: Main body structure for an interplanetary landing craft.
CUSTOMER: Autodesk.
The structure was optimized for minimum mass using Autodesk prototype generative design software and Fusion 360. The concept interplanetary lander was designed for travelling enormous distances to the moons of distant planets such as Saturn and Jupiter. The principal challenge was its hollow structure with a typical wall thickness of 3mm. TEI worked closely with Autodesk to position adequate core supports throughout the hollow casting in areas that their finite element analysis (FEA) showed were not highly stressed. Simulation was used extensively for the mold filling and solidification.
OUTSTANDING ACHIEVEMENTS
Pump Housing: O'Fallon Casting
MATERIAL: C355-T6.
PROCESS: Investment casting.
WEIGHT: 9.6 lbs.
DIMENSIONS: 12 in x 10 in x 8 in.
APPLICATION: Pump housing for aerospace.
The number and complexity of the internal core passages in this casting allow the customer to decrease the overall size and number of pieces in the engine pump. Instead of multiple pieces with less complex geometries being assembled together, this one piece investment casting saves weight and eliminates future failure points at the assembly location. The pump casting contains 12 interconnected core passages throughout the inside of the casting, with varying diameters and depths. The combination of thin walls in certain areas, large masses of metal in others and the grade B metallurgical requirements make this casting a challenge, something ideally suited for the investment casting process.
Drone Frame: Aristo-Cast
MATERIAL: Magnesium.
PROCESS: Investment casting.
WEIGHT: 0.628 lbs.
DIMENSIONS: 11 x 11 x 4.25 in.
APPLICATION: Lightweight video/delivery/inspection for aerospace.
CUSTOMER: Autodesk.
Lighter drone frames can stay in the air longer, and drone frames created in metal are stronger and more durable than plastic frames. Using generative design software, Autodesk created a drone frame design that would reduce weight and maintain the required strengths. The design would be impossible to create through conventional methods of creating patterns for castings or to injection mold the frames in plastic, therefore additive manufacturing was needed to print the patterns for the investment casting process. The generatively designed frame coupled with the material change to magnesium reduced the overall weight by 50% from the original design, while it maintained the strength required to perform the tasks. Just the material change from aluminum to magnesium saved 35% in overall weight.
T1XX Side Door Mirror Reinforcement Bracket: Magna Cosma Casting Michigan
MATERIAL: Aluminum alloy 5S – F temper.
PROCESS: High pressure vacuum diecasting.
WEIGHT: 1.31 lbs.
DIMENSIONS: 14.5 in x 6.4 x 15.4 in.
APPLICATION: Attachment points and load carry for large side door.
CUSTOMER: General Motors.
The light duty side door mirror reinforcement bracket is a single piece, vacuum diecast aluminum Aural 5S alloy F (as-cast) temper casting. The aluminum casting provided engineers with more design flexibility and more efficient attachment points. This casting replaces a traditional five-piece aluminum stamped and welded assembly with a mass savings of 20% (37% mass savings over a steel design) while improving the stiffness at the weak point of the side door window frame.
Front Bracket Extension: Monarch Industries
MATERIAL: D100-70-03 ductile iron.
PROCESS: Green sand.
WEIGHT: 94.6 lbs.
DIMENSIONS: 25.1 in x 13.7 x 21.8 in.
APPLICATION: Multi-functional frame rail mount for vocational trucks.
The previous generation part was a weldment that had similar form but a significant number of parts that were difficult to fixture together. It also was susceptible to warpage and corrosion where stiffener plates overlapped existing surfaces. The original weldment contained no less than 17 distinct pieces. The customer reported that the new cleaner, simplified casting design provided a 43% reduction in cost over the original weldments. The casting simplifies the fabrication significantly without the need for highly skilled labor, namely qualified welders, resulting in improved lead times and reduced delays and fabrication bottlenecks during labor shortages.
Opener Frame: Lethbridge Iron Works
MATERIAL: Ductile iron ASTM A536 65-45-12.
PROCESS: Horizontal green sand.
WEIGHT: 68 lbs.
DIMENSIONS: 36 x 16 x 8 in.
APPLICATION: Frame for mounting seeding components.
The serrated teeth were originally achieved by bolting a separate casting to the fabrication. The final casting design incorporated the serrated teeth and therefore eliminated the need for a separate bolt on casting. The original design’s length limited the number of impressions in a mold that resulted in the conversion not being cost effective. A collaborative redesign reduced the casting size and allowed for a multi-impression pattern.