Why Can't I Get My Castings Tomorrow
Casting buyers face many challenges to getting the castings they want, when they want them. Probably the biggest one from a new buyer’s perspective revolves around the time it takes to produce a casting.
Purchasing agents often ask, “why does it take so long to make my castings?” Buyers often compare suppliers of different commodities and generalize that they should have similar manufacturing times. This thought pattern can often leave buyers puzzled when they discover they can’t get castings made and delivered in a few days when their need becomes pressing.
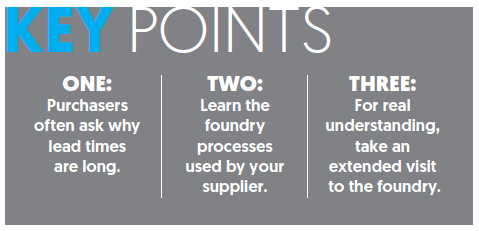
To help in the understanding of required time, let’s take a high-level look at the green sand casting process. Green sand molding is one of the most common and widely used sand casting processes available. Other casting production processes may have slightly different nomenclature for the steps in the process, but they will be similar
The first step is making cores for your casting. This will take anywhere from a few hours to a few days depending on the size of the core and the process used. If the core needs to have a refractory coating applied, additional time will be required for application and drying.
Molding would be the next step. This can proceed efficiently if automated processes are used, but it could take up to several hours if the mold size is large or there are complex core setting procedures to follow.
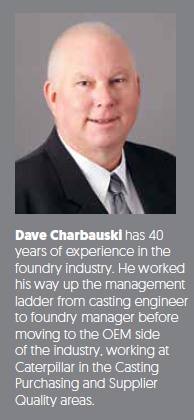
After the mold is closed it is moved to the pouring area. Pouring itself does not take very long, so the time factor encountered here is in cooling time after the mold is poured. Cooling is relatively quick with small parts but can take up to several days for large castings. Another factor to consider revolves around your metal specification: is it poured on a daily basis or does it require a unique chemistry and is only periodically scheduled based on accumulated demand?
Once cooled, shaking out the casting from the mold, riser removal and initial shot blast are straightforward. Grinding, finishing and packaging are the final steps and the time for this will vary depending on the amount material that needs to be removed, finishes required (paint, etc.) and shipment requirements. Keep in mind that there are also quality checks at various points throughout all the casting processes that can add additional time.
You may ask if your order can be expedited. A point to consider is there are queues for most every step of the processes listed above, so you are bound to encounter some waiting time. Expediting your order can sometimes be done, but it usually comes with a cost, and should only be done when it is absolutely necessary. Remember that every time you push to expedite an order, you are effectively cutting in line in front of other casting customers. How often would you want that done to you?
It quickly becomes apparent the key step in gaining the knowledge of how long it takes to make a casting is to develop a deep understanding of your casting supplier’s manufacturing process. This is an extremely important step in your buyer training; don’t be tempted to take shortcuts when it comes to learning the process.
In my experience, the best way to learn the process your casting supplier uses is to make a visit to their foundry. Instead of taking a quick shop tour, schedule an extended visit with your supplier and go through each process step in depth. My recommendation is to plan on spending several hours in each of the departments.
You’ll be amazed at what you will learn, and you will gain a new level of respect for what the foundry does to produce a high-quality casting. An additional benefit to this extended visit is that you will also grow your relationship with the foundry, which is vital to developing long term success. Start the planning now so you can implement this into your annual training goal.
Click here to see this story as it appears in the November/December 2019 issue of Casting Source.