Materials Properties 101: Strength
Even as far back as Ancient Rome, steel was prized for its ductility and strength. Steel alloys are still in high demand today, and it’s primarily the same properties—strength and ductility—that make steel alloys so important for modern manufacturing. Likewise, the importance of strength as a metal property has not changed: knowing when any metal will begin to stretch, deform, and break is vital to understanding how it can be used.
Materials scientists and engineers commonly use two metrics to predict how a metal will withstand conditions of stress and how well it will resist breaking: yield strength (also known as upper yield point) and tensile strength (also known as ultimate tensile strength). In the English and American system of measurement, strength measurements are designated in pounds per square inch (psi). You may also see them denominated in Pascals (Pa) or Megapascals (MPa) in the metric system.
How Do We Measure a Metal’s Strength?
The chart in Figure 1 illustrates a tensile strength test on a material. The y-axis (vertical) represents stress, which is the force applied to the material. Strain is represented on the x-axis, which describes the change in length (or deformation) due to the applied force. In the case of a tensile test, we usually want to measure the metal’s resistance to being pulled or stretched, so imagine stress applied by two vices clamped on the ends of a metal rod pulling in opposite directions. The graph in Figure 1 shows how much the rod elongates as it is pulled harder and harder in opposite directions. Note that at certain points changes occur in the relationship between the amount of stress and the resulting degree of strain.
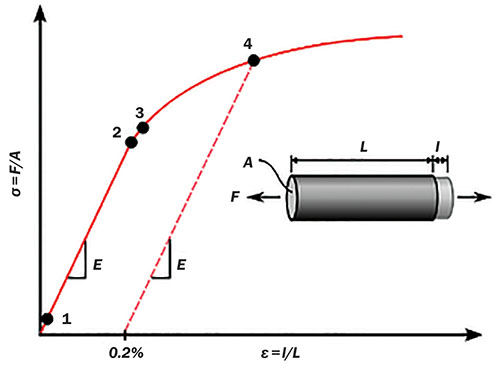
The first phase is proportionality, where there is a linear relationship between the amount of force applied (stress) and the amount the metal elongates (strain). During this phase, any changes to the shape of the metal are only temporary; when the force is removed, the metal rod will return to its original shape. In physics lingo, temporary changes are called elastic deformation.
The next phase is plastic deformation. When the line starts to curve after Point 3, the material will not return to its original shape. Elastic deformation is expected to some degree in all metal parts, but plastic deformation often leads to part failure. That’s one of the reasons strength is so important to cast and machined metal parts.
How to Measure Yield Strength
Manufacturers are primarily concerned with that transition between elastic and plastic deformation. Understandably, our customers want to know how much force a material can withstand before it fails to return to its original shape. Yield strength can be measured by applying enough force to produce 0.2% of plastic deformation. In Figure 1, this is Point 4, and yield strength is the amount of force it takes to reach that point. This measurement is often listed as a standard reference in the ASTM standards.
How to Measure Tensile Strength
The graph in Figure 2 is another stress/strain curve illustrating ultimate tensile strength. Remember that all deformations after the yield point (“yield stress”) are plastic, meaning the changes in shape are permanent. After the ultimate tensile point (UTS), the alloy bar begins to fracture. Simply put, tensile strength signifies the maximum amount of stress a material can withstand before breaking. In most cases, this is far beyond what would represent actual part failure, but UTS is still a key metric used when choosing the right alloy for each product.
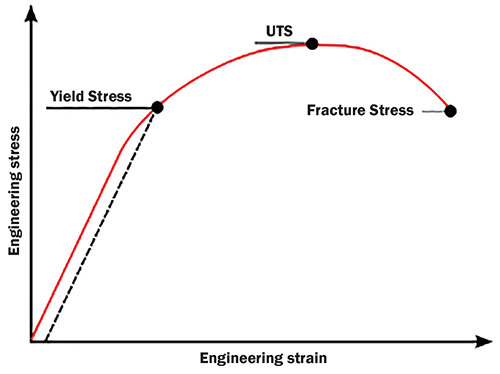
Measuring Strength in Cast and Machined Metal Parts
Measuring the strength of an actual product is not the same as measuring the strength of an alloy bar. In fact, part strength relies much more on theory than real-world testing. Planning for the strength of a part starts early in the design phase. Casting providers work with their customers through an extensive APQP process where the foundry engineers ask questions about part performance and operational environment to ensure that the customers’ designs will lead to functional, manufacturable products. This process also helps casting buyers—often with guidance from the foundry—select the ideal alloy for each part.
Knowledge of material strength comes from resources like the ASTM standards, but it also comes from hands-on experience producing cast and machined metal parts. Each part is like a case study that helps a foundry understand what works best in each unique situation.
At Eagle Alloy, if a customer requires further verification, tests can be performed in-house, such as a hardness test on the actual cast part. While hardness and strength are not the same, there is a strong correlation between the two mechanical properties. In-house testing can also include casting a bar in any alloy and performing destructive tests on it, much like those illustrated in the stress/strain curves. This helps determine whether an alloy the foundry plans to use for a part conforms to the customers’ performance requirements.
Why Yield Strength and Tensile Strength Are Important for Metal Manufacturers
In machine shops like Eagle CNC and foundries like Eagle Alloy and Eagle Precision, yield strength and tensile strength are crucial data points and figure heavily into the overall design of every product. Casting buyers often bring product designs and specific needs for metal properties. While foundries typically are not design-responsible, they will work with the customer to choose the best alloy that will achieve their desired properties while maximizing efficiency in the manufacturing process.
Looking at the manufacturing process holistically, it’s more than just the material being cast that determines properties like strength. Foundries must closely control the material chemistry, handling, processing, and heat treatment that produce the material to meet the customer’s defined properties.
Once the cast parts are working in the field, their yield strength is put to the test. These parts often fit into more complex systems, and industrial products like valve bodies, tractor parts, and rail ties undergo a broad range of stresses during everyday use. Components in any machine are expected to temporarily stretch or bend in fractional increments, as long as they don’t permanently deform or break during use.
Tensile strength also plays a major role in safety. If a component suffers an outsized impact load due to fire, earthquake, occupational accidents, or other hazards, the plasticity of a metal is often responsible for absorbing the excess load, preventing a potentially dangerous situation. Whereas yield strength will make sure a part or appliance continues to work, tensile strength will make sure no one gets hurt. CS
Jason Bergman is quality manager and metallurgist at Eagle Alloy. He has been with the company since 2013. You can read more of Bergman’s articles about metal properties and more at
blog.eaglegroupmanufacturers.com.