Avoiding the Double Doink
The ball careened into the left upright, fell nearly straight down, and bonked off the cross bar in the wrong direction as the final seconds ticked down in the Philadelphia Eagles/Chicago Bears first round playoff game. Almost immediately, the missed field goal that cost the Bears the game was referred to as the “double doink.”
Part of the pain for Bears fans was the kicker’s regular season kicking history. His field goal percentage was one of the worst of the league and he was tied for the most missed field goals in the regular season with seven. He also missed three extra point attempts. Our associate editor Brian Sandalow texted me later that night, “So predictable. Like out of a script. A horror script, but a script nonetheless.”
Red flags had been raised, and the signs were there. Based on previous performance, the Bears kicker was at more risk to miss, and eventually it ended the team’s season.
Are you in danger of a double doink?
Are there components in your designs or machinery that are failing more than others? Are there parts that are expensive to make but ignored because the rest of the equipment is performing well? Is there a piece that requires more inventory due to lead times?
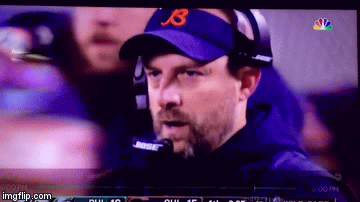
In a complex system of components, it is difficult and perhaps even unnecessary to have everything designed and sourced perfectly, but what are you risking?
If the part fails in service, will it cause monetary damage or put someone in danger? If one component is expensive, will the loss in profit hinder expansion into new applications? If the delivery of a piece blows past the expected date, will that prolong the whole project’s schedule, and how much will that end up costing?
The answer to a problematic part can be wide-ranging, from sourcing to a different supplier to changing the design. Switching to another manufacturing method is also an option. This was the case for the tube clamp on page 17. The original weldment was a seemingly simple component in a piece of farming equipment but it was costing the manufacturer a lot of money, taking up labor time and causing deliveries to drag.
The equipment manufacturer recognized it was time to address the issue before the cost of these annoyances torpedoed the project. By changing the manufacturing process to metalcasting, inventory and lead time delays were reduced and the company saw a 60% cost reduction. They avoided a double doink.
Direct conversations with metalcasters can help you decide whether switching your existing fabrication to metalcasting would solve many of your issues. Call up your foundry supplier and tour the shop floor if you can. Do you see castings in production there that mimic the same shape or function as your weldment? That might be a candidate for casting.
Another opportunity to meet with foundries is coming up in April at CastExpo 2019 in Atlanta. The metalcasting trade show is offering the chance for casting designers and buyers to BYOB (bring your own blueprint) to discuss with foundry personnel. Bring your problem job and see—could it be a casting? Would converting to casting reduce your risk? More information and registration is at www.castexpo.com.
The Bears (and their fans) knew their kicking game was not great, but they hoped it would be good enough. Don’t wait too long to fix your known problems. A minor nuisance now can turn to catastrophe (and embarrassment) later.
Click here to see this story as it appears in the January-February 2019 issue of MCDP.