Using In-Process Welding to Repair Aluminum Castings
Most aluminum foundries employ welding for legitimate activities, like welding a plug into a core support hole, but it is also often used to repair defects in castings so they meet dimensional or other quality specifications.
Neither customers nor foundry management are completely comfortable with this, since the mantra is to make it right the first time. Nonetheless, complicated designs, low volume requirements or cost pressures sometimes make it necessary to use weld rework to salvage castings.
Castings are susceptible to having small surface imperfections such as inclusion pits, gas microporosity, cold laps, misrun edges, or dents from handling damage that are cosmetically unappealing or non-compliant. In-process weld rework of castings is a routine casting finishing activity that is used to mend such casting surface imperfections across almost all alloy families and mold cavity-making processes.
A casting that has been welded, blended, and heat treated and has passed all drawing specified inspections will be dimensionally, physically, chemically, metallurgically, and structurally compliant to drawing requirements. Therefore, specifications to limit or document in-process weld rework of surface imperfections are rarely noted in commercial castings.
What the Specifications Say
For military and aerospace castings, the severity of cast component service is classified (Classes 1 through 4) and surface and/or internal integrity is specified by AMS 2175, Grades A through D. Classes require different levels of nondestructive testing, and grades directly affect allowable stress for cyclic life. AMS 2175 covers almost all casting processes and the full range of casting alloys, so it is also adopted as a commercial standard for safety-critical castings.
Importantly, AMS 2175 is silent regarding in-process weld rework, only specifying the extent of imperfection in Grades A through D as “graded” in visual, radiographic, magnetic particle, or die penetrant inspection. This is inspection after all as-cast processes are complete, including final heat treatment.
Logically, castings that are classified 1 or 2 should have carefully defined specifications for in-process weld rework. Such specifications and/or drawing notes define the weld processes, weld filler alloys, pre-weld surface preparations, welder qualifications, post-weld surface blending, and pre-weld and/or post-weld heat treatment. The manufacturing capability of these specifications to sustain class and grade’s strain life properties has been established by data developed by OEMs, defense primes, and metalcasters. Some data has been published, but much is considered proprietary and not generally available.
The most limiting specifications, typically AMS-A-21180 and its ASTM counterparts, may call out “no-weld zones” or “in-process weld rework only upon written permission of the purchaser.” Maps may be required showing location, size, and depth of welds. No structural component of any kind and, therefore, no structural casting, is critically stressed all over. This scenario, best represented by specification AMS-A-21180, should be applied only to casting surfaces that really are critically stressed.
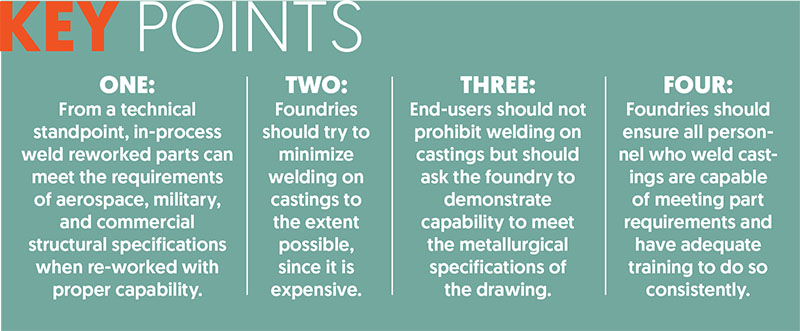
Other specifications give direction on repair welding of aluminum castings that are sometimes used. AMS 2694 defines requirements for in-process corrections of discontinuities by manual welding. Several specifications deal specifically with welding of aerospace structures such as AWS 17.1 and FAA Advisory Circular No. 33-6 on weld repair of aluminum crankcases and cylinders.
Property Studies on Weld-Repaired Castings
In an early study of the efficiency of repair welding of aluminum casting, A357-T6 and A201-T7 material which had been welded to a depth of 50% of the wall thickness were re-heat treated and tested for notched fatigue, fracture toughness and tensile properties. Compared to the properties of the parent material, the tensile properties of the welded material of both A357-T6 and A201-T7 were very similar, and the notched fatigue and fracture toughness of the welded A201-T7 were better than the parent material. The fatigue properties from welded A357-T6 material showed a slight degradation compared to the parent material after 500,000 cycles, and the fracture toughness properties of welded A357-T6 were similar to the toughness of the parent material.
A more recent study showed that properly accomplished in-process weld rework had essentially no effect on the static and dynamic tensile properties of E357-T6 sand castings. This work was done with sand cast plate, with a defect machined in to duplicate either a full weld or a half weld repair. Figure 1 illustrates that concept, and Table 1 shows the summary tensile data.
The fatigue data for the three types of specimens (Figure 1) are very similar to each other. However, regression suggest that the cast (no weld) specimens are slightly better (longer life) at high stress levels, the full weld and no weld specimens are about the same life at low stress levels, and the half weld samples demonstrated the longest fatigue life at low stress levels. This suggests either a difference in the microstructure, the geometry of any pores present, or the number of pores present in the original cast structure of the metal in the weld zone. CS
What's Going on During Weld Rework?
Welding is another molten metal process. The correct manufacturing steps can be defined, and the details will depend on the specific defect. The supplier performing the operation should follow these key steps to achieve high
quality welds:
- Prepare the weld area. Remove the defect and remove the oxide layer with a brush or solvent.
- Preheat before welding. Preheat generally improves welding results. Castings will usually be welded in the as-cast condition but sometimes defects will not be uncovered until after heat treatment, so they are welded in the T6 or T7 condition. In 200 series alloys or for castings that require extensive repairs, it is recommended that T6 or T7 tempered castings be annealed before welding to avoid cracking.
- Use weld rod that matches the chemistry of the casting or an approved substitute. Chemistry control in welding is as important as it is in melting for casting. Use of a general-purpose rod across all alloy systems will result in reduction of mechanical properties and color mismatches even though welding may be “easier.”
- After welding, the weld needs to be dressed back to part contour. If a weld repair is noticeable with casual viewing, the repair has not been done correctly.
- Heat treat after welding. Even though a good weld will have little porosity and a fine structure, mechanical properties will not be met if the repaired casting is not heat treated to the specification. Heat treatment will also eliminate the residual stress that may have been caused by the welding process.
Click here to see this story as it appears in the March/April 2020 issue of Casting Source.