Experience Paves Way for More Casting
AerWay, a division of SAF Holland that produces agricultural tillage equipment, has performed multiple forging-to-casting conversions and achieved benefits from those efforts. With this experience and through collaboration with AFS Corporate Members Urick Foundry (Erie, Pennsylvania) and Applied Process (Livonia, Michigan), the company determined another family of forged and fabricated parts were good options for casting—trunion brackets and trunnion bracket guards. CS
BEFORE
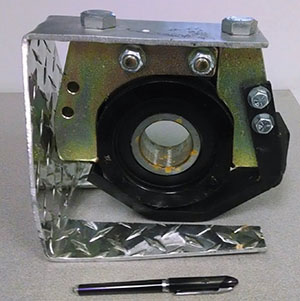
The original trunnion bracket was machined from carbon steel barstock (CSA G40.2144 W carbon steel). The trunnion bracket guard was a piece of bent steel with two steel ears welded on. One bracket was mounted to the implement, and the mating bracket was assembled to the guard with four fasteners. Together they surrounded a bearing.
AFTER
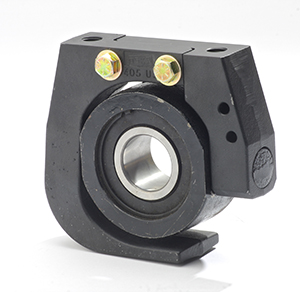
The engineering team turned one of the trunnion brackets into a 80-55-06 ductile iron casting and the other bracket and guard to a one-piece ADI casting. During the redesign, the natural flowability of ductile iron was exploited to minimize section size and reduce the need for expensive alloying in advance of heat treatment. This work reduced part weight, which alone was a cost reduction, but it also reduced manufacturing burdens associated with maintaining separate return streams in a production foundry. The newly redesigned part featured an elegant design with weigh- and cost-saving improvements over the first draft. This design takes advantage of the ductile iron casting process to put material where it is needed and remove material from where it is not. Further, the material choices were optimized for cost control because the regular ductile iron trunnion bracket did not incur the cost of heat treatment while the more demanding trunnion bracket with guard was appropriately austempered.